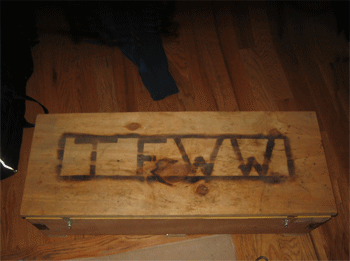 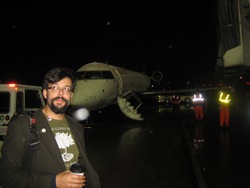
I wrote this entry in an airplane cruising over the clouds as Tim and I headed home to Brooklyn from Woodworking in America.
One week ago, after leaving work at midnight because we were finishing up the new Gramercy Tools Kings County Hammer, I rushed home to pack my underwater-camera and some socks before flopping into a cab for the ride to LGA.
Tim and I arrived in Cincinnati a little bleary eyed but enthusiastic. Our first official work event was the Bloggers Beer Bash. It was a hoot, but the next morning as I walked past Roy Underhill with my pile of bacon and coffee we had this exchange:
"Oh, you look fresh, you wern't out with Tim last night?"
"Huh, No, I mean yes... what?" (I look over at Tim huddled around his third cup of coffee and gently groaning into his untouched breakfast)
Roy peers into my eyes...
"Ahhh yes. I can see it now, you just hide it better."
er.... thanks Roy?
Running the booth was a lot of fun, but didn't leave much time to look around. I tried my best to walk around a bit and check out all the sweet stuff while not abandoning my co-worker. Here's my run-down of the coolest things I saw/did:
The Sauer and Steiner K13 has been all over the web, but seeing it in person was sweet, and when Konrad Sauer handed it to me to try I couldn't believe it. The plane cut a gossamer shaving. It was startlingly smooth and of course had that bombproof infill feel. It also looks like the million bucks it must have cost. I would give a fuller assessment but I'm not allowed to use the necessary language in this blog.
In other news Matt Bickford's planes are some of my faves. The conical escapement on his rabbet and side round planes is both traditional and amazing. It's walls twist like a cherry ribbon gracefully encasing the mouth and the iron. Now if only he used a year stamp like Old Street...
While I'm geeking out on wooden tools, I want to mention a v. v. nice antique vice brought to the show by Jameel Abraham of Bench Crafted. At first I thought it was an unusual mill vise made of wood. Jameel corrected me and said that although it looks similar it is a carvers vise... perhaps I can mount one on the Bridgeport...
I tried my first Bad Axe Saw. Mark called me a spy every time I had my camera out, but honestly, I was more interested in the color combinations he offers than how he makes his saws because I already know his secret: Attention to detail, high quality components, and giving a damn. A few people now have asked me if a Bad Axe is nicer than a Gramercy. I don't know if an answer is possible, and it's not just because I know which side my bread is buttered on. Bad Axe and Gramercy are different styles. The Gramercy is built to be light and nimble while the Bad Axe has the Ker-chunk of a firearm. They both cut so well you have only yourself to blame. I think that in the competition between the contemporary saw makers the only folks winning are the customers. Y'all have your choice of the best hand saws ever made!!! And now thanks to Bad Axe you can even have your back saw murdered out. Hand tool renaissance much?
I finally got to see a real live Bridge City Tool, a first for me. John Economaki showed me his take on the shoulder plane, which uses a clever toggle clamp to hold the blade in place. He also confided in me that he is pretty sure he can computer render anodized aluminum so well that no one can tell its not a photo. Which begs the question: if a plane is anodized in the forest and no one sees it...
The metal tool to wooden tool cross-over was (for me) best exemplified by Lie Nielsen's new No. 81 Spoke shave. Its shape is a little reminicent of the Kansas City Windsor Tool Works spokeshaves (RIP) which I own and love, but I have to say that I prefer the Lie Nielsen. I use my spoke shaves pretty heavily some times, but they feel like the blade is bending when I try to take too deep a cut, the Lie Neilsen felt rock solid even as I accidentally shaved against the grain of a piece of walnut and tore off a goodly sized chunk wood.
After trying to break the Godfather's new tool I was feeling a little sheepish, but luckily Michael Auriou is the type of guy who makes you feel like you're doing a good job. In addition to running an eponymously named and GREAT, tool company, he's just a friendly dude. Tim surprised me with a special treat, by asking Michael to show me how to hand punch a rasp. I learned the proper punch holding technique (detailed here) and started punching. MAKING A RASP IS SOOO HARD, but Michael was encouraging and told me I did a good job to which I said "Merci, c'est Super Cool" in my best french accent.
Speaking of French accents, Tim and I put on our suits to attended the Roubo Society Dinner. During the dinner Tim and I had the unexpected pleasure of sitting next to Peter Follansbee, which was awesome because he, like Roy Underhill, is one of those folks who makes me excited about human potential.
All in all the show was really wonderful both because of the well crafted tools on display and the folks making and using them. Tim and I were super stoked on meeting/catching up with so many customers, comrades, and compatriots. As a tool maker I'm honored to be a part of the small community of folks dedicated to hand tools. It was great to meet everyone, and if you are ever in Brooklyn come visit us!
|
Lloyd
Keep up the good work with the blog, its looking great!
Wish I had another way to get a hold of you(you'll remember me if you visit my website I think). We should get together mang! I'm working on a few things I know you'll be into. Later.
The link is correct, although it's a joke/Easter egg because the hand position for holding the rasp punch looks a lot like a cross between the Bloods and Crips hand signs, and this being Brooklyn and all....
The actual technique is detailed on our website here:
https://toolsforworkingwood.com/store/more/AU-Hist.html